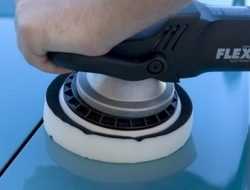
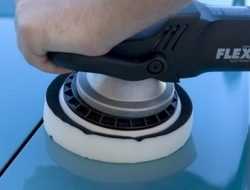
Чтобы добиться блестящей поверхности металла, необязательно материал покрывать лаком. Можно прибегнуть к полировке металла, что используется как декоративный вид обработки детали после нанесения покрытия или в процессе обработки изделия. В одном случае достаточно опилить металл напильником, в другом — поверхность следует довести до блеска путем электрополировки. Все эти манипуляции можно сделать самостоятельно в домашних условиях.
Содержание:
- Предназначение полировки
- Достоинства электрополировки металла
- Электрополировка с использованием кругов
- Электрохимическая полировка
Предназначение полировки
Детали из металла имеют изначально гладкую блестящую поверхность. Но она со временем тускнеет и в процессе эксплуатации царапается. Для скрытых деталей, безусловно, внешний вид не имеет большого значения, но когда металлические детали располагаются на виду, то они должны выглядеть должным образом. Именно так будет смотреться глянцевая поверхность, после того, как вы провели полировку металла.
Полирование металлов предназначается также для улучшения гладкости и чистоты поверхности металлических деталей и устранения следов прошлых обработок – неровностей, царапин и вмятин. Полировку деталей проводят с помощью наждачных кругов, шлифовального порошка, специальной известковой пасты, полировочного раствора или электролита.
Поверхности металлических деталей отделывают не только с целью придания им привлекательного внешнего вида, но и чтобы защитить от ржавления, разъедания щелочами и кислотами. Хорошо полировке поддаются такие металлы, как латунь, бронза и медь. Нержавейку до зеркального блеска не получится довести, а вот придать ей матовый глянец – запросто.
Исходя из вышесказанного, можно утверждать, что полирование бывает двух типов – предварительное и окончательное. Предварительную полировку металлов применяют при механическом удалении неровностей, а окончательную – для создания идеально ровного и глянцевого финишного состояния металлической поверхностей и защиты её от неблагоприятных факторов внешней среды.
Достоинства электрополировки металла
Отдельной веткой полирования является электрополировка стали. Процедура оказывает благоприятное влияние на физико-химические, электрические и магнитные свойства металлических поверхностей, облегчая глубокую вытяжку и штамповку определенных металлов, а также увеличивает уровень их коррозионной стойкости. Этим объясняется широкое применение электрополировки при лабораторных исследованиях металлов и в промышленности.
Электрополирование имеет целый перечень преимуществ перед механической полировкой в отношении простоты, универсальности и скорости. К примеру, нержавеющую сталь механическими методами трудно полировать, так как это длительная и дорогостоящая операция. Электрополировка нержавейки же происходит на протяжении нескольких минут, является дешевой процедурой и позволяет получить поверхность с лучшими отражательными способностями.
Электрополирование уменьшает время обработки изделия по сравнению с механической технологией почти в 5 раз, хотя и повышает чистоту поверхности всего на 1 - 2 класса. При механическом полировании можно добиться высшей чистоты поверхности, однако процесс электрополировки незаменим при обработке изделий сложного профиля с внутренними полостями, деталей топливной системы дизелей и пружин, которые являются неудобными и сложными по форме для механической обработки.
Электрополировка является самым лучшим методом подготовки поверхности перед нанесением гальванического покрытия, потому что демонстрирует высокую прочность сцепления защитного покрытия с отполированной основой. Данную методику применяют для обработки деталей для улучшения скольжения материалов, которые соприкасаются с полированной поверхностью, к примеру, нитеводители в текстильных машинах, для заточки режущего инструмента при производстве мерительного инструмента.
Электрополирование, кроме устранения трудоемких и вредных механических операций шлифования и полирования, ликвидирует затруднения, которые вызываются твердостью или вязкостью полируемого изделия, и операции обезжиривания изделий, что крайне необходимы при механическом полировании. Высокая производительность процедуры при этом не зависит от твердости металла. Электролитической полировке одинаково хорошо поддаются алюминий и мягкая красная медь, закаленная цементированная сталь и инструменты из твердого сплава.
Недостатком является увеличенный расход электроэнергии. Некие неудобства связаны с тем, что практически каждый металл требует своего состава электролита. Продолжительность процесса зависимо от плотности тока достигает 20 - 30 минут. Обычно при таких манипуляциях снимается слой металла, что имеет толщину 2 - 5 мкм.
Электрополировка с использованием кругов
Для шлифовально-полировальной работы принято использовать специальные полировальные станки с валом электрического мотора, который с обеих сторон удлинен для закрепления полировального инструмента. Подобные станки имеют регулятор, который позволяет регулировать частоту вращения щеток и кругов в значительных пределах.
Полировальные диски
Изделия и детали, которые подлежат электрополировке, не должны иметь слишком глубоких рисок и царапин, потому что вывести их с помощью данной методики чрезвычайно трудно, а зачастую почти невозможно. Помните, чем мягче металл, который подвергается полировке, тем легче с него снять слой, но сложнее достичь однородной поверхности. Полирование твердого металла принято проводить с большим удельным давлением на обрабатываемую поверхность.
В качестве полировальных кругов применяют войлочные диски, диски из кожи, шерсти и хлопчатобумажных тканей. Для механического полирования берут щетки, изготовленные из щетины и латуни. Для подобного полирования дополнительно используют смеси или суспензии. Обычно для полировки металла необходимо два круга – войлочный диск для грубой полировки и тканевый для тонкой.
Войлочные полировочные диски для электрополировки нержавейки или алюминия представляют из себя несколько слоев войлока, которые имеют толщину до 4 сантиметров, скрепленных между собой клеем. Слои войлока при изготовлении шлифовочного диска плотно прижимают друг к другу и ставят под пресс.
После того, как они приклеятся, и клеящий состав высохнет, принято проделывать в середине круга отверстие. После этого круг закрепляют на валу электроточила при помощи двух гаек с шайбами. Подобный шлифовальный круг также легко закрепляется в патроне сверлильного станка или электродрели.
Матерчатый диск можно вырезать из хлопчатобумажной ткани, сукна, миткаля или бумазеи, после чего сшиваются слои диска вместе в несколько слоев. Сшитые круги нужно склеить между собой, оставляя по краю 3-4 сантиметра. Диск насаживают на патрон сверлильного устройства таким способом, как и крепился войлочный диск.
Рабочий процесс
Прижмите металлическую поверхность к вращающемуся диску, чтобы начать процедуру электрополировки в домашних условиях. Рабочую поверхность кругов при полировании рекомендуется периодически смазывать специальной полировальной смесью, причем в определенной дозировке.
Помните, что круг будет «салить» деталь при избытке смеси, при её недостатке круг быстро износится, а металл не получит желаемого блеска. Поэтому при смазывании полировальных кругов свободной от полировальной смеси оставляйте примерно четверть рабочей поверхности.
Эластичные круги должны вращаться и прижиматься к деталям с определенным усилием, сама полируемая деталь должна по отношению к кругу свободно передвигаться. Электрополировку с применением смесей можно осуществлять торцом или периферией круга. Перемещение изделий производят непосредственно особым приспособлением или рукой.
Частота вращения круга на полировальном станке составляет 2000—2800 оборотов в минуту. Полировальные станки с большой частотой вращения кругов используют, когда требуется значительное качество обработки. Для достижения зеркального блеска электрополировку алюминия осуществляют при более низких частотах.
Если изделия, которые предстоит подвергнуть воздействию полировки, имеют простую форму — плоскую или квадратную, то вы можете их обработать на универсальном электрическом станке, где установлен полировальный круг прямого профиля. Для проведения грубой обработки предназначены твердые и жесткие круги, для тонкой — мягкие.
Твердые круги интенсивно полируют, но быстро засаливаются, особенно при обработке мягкого цветного и драгоценного металла или его сплава. Мягкие эластичные круги малоэффективны на предварительных операциях и способны деформироваться и расплющиваться при сильном прижатии к обрабатываемой детали.
Периодически отнимайте диск от металлической детали для оценки качества создаваемой полировки. Когда внешний вид металла вас удовлетворит, а деталь станет идеально гладкой, блестящей и ровной, можно остановить процесс. После этого повторите процедуру на тряпичном диске, который способен снять с поверхности металла остатки полировочного вещества.
Электрохимическая полировка
Электрохимическое полирование представляет собой процесс, который характеризуется химическими реакциями между обрабатываемым изделием и электролитом под действием электрического тока. Эта процедура приводит к уменьшению шероховатости и возникновению зеркального блеска.
Микро- и макро-полирование
Для проведения электрохимического полирования обрабатываемое изделие, которое является анодом, соединенным с плюсом источника тока, помещают в ванну с электролитом. Второй электрод – медные катоды. Благодаря специальному составу электролита для электрополировки и созданным условиям (формирование пленки повышенного сопротивления) фиксируется неравномерное растворение.
В первую очередь будут растворяться наиболее выступающие точки, вследствие чего уменьшается шероховатость, а потом исчезнет совсем, и поверхность детали станет блестящей и гладкой. Избирательное растворение подобных торчащих элементов протекает одновременно с получением блеска.
Процесс удаления больших выступов называют макро-полированием, а растворение малых неровностей - микро-полированием. Если эти два процесса протекают одновременно, то поверхность металла будет приобретать гладкость и блеск. Бывают ситуации, когда данные качества являются друг с другом несвязанными, то есть блеск достигается без сглаживания и наоборот.
В процессе электрохимической полировки на поверхности анода образуется гидроокисная или окисная пленка. Если она покрывает поверхность равномерно, то создаются условия, что необходимы для микро-полирования. Внешняя часть подобной пленки будет непрерывно растворяться в электролите.
Поэтому для успешной процедуры требуются условия, в которых существует равновесие между скоростями формирования окисной пленки и ее химического растворения, чтобы толщина пленки была неизменной. Наличие пленки подразумевает возможность совершения обмена электронами между полируемой деталью и ионами электролита без риска разрушения агрессивным электролитом металла.
Процесс макро-полирования зависит от наличия прианодной пленки, которая является более толстой в углублениях и тонкой на выступах. Подобная пленка способствует быстрому растворению выступов, потому что на них создается высокая плотность тока, а электросопротивление над ними будет меньше, чем над различными углублениями.
Эффективность действия прианодной пленки увеличивается с возрастанием ее внутреннего сопротивления. Электролиты, которые содержат комплексные соли или соли слабодиссоциирующих кислот, способны повышать сопротивление прианодной пленки.
Электролиты и растворители
На течение процесса электрополировки кроме прианодной пленки оказывают действие и другие факторы, такие как движение анода, что состоит в механическом перемешивании электролита. Электролиты некоторого состава способны нормально функционировать только при нагреве. Общее правило кроется в следующем: увеличение температуры способно снижать скорость нейтрализации и повышать скорость растворения пленки.
Значимыми факторами, которые влияют на течение процедуры электрохимической полировки, выступают напряжение и плотность тока. Зависимо от обрабатываемого металла и состава электролита принято вести полирование при режимах, которые соответствуют разным участкам кривой. К примеру, полировку меди в фосфорной кислоте проводят при режиме предельного тока без образования кислорода.
Самое большее распространение получили электролиты, изготовленные на основе серной, хромовой и фосфорной кислоты. Для увеличения вязкости раствора в него вводят метилцеллюлозу и глицерин. В качестве ингибиторов травления принято добавлять в электролит триэтаноламин и сульфоуреид.
Для очистки изделий после процедуры электрополировки принято использовать растворители, которые изготовлены на основе хлорированных углеводородов — перхлорэтилен и трихлорэтилен.
Эти вещества являются негорючими, их способность к удалению паст и жировых загрязнений с изделий выше, чем у этилового спирта или бензина. Изделия нужно загрузить в ванну, обработать мягкой волосяной щеткой, перегрузить в сосуд с нагретым нашатырным спиртом, где удаляться остатки паст и жир.
В качестве щелочного моющего средства применяют щелочи (едкое кали, едкий натр), поташ, соду и нашатырный спирт. В последние годы популярностью все больше пользуются моющие составы на основе всевозможных поверхностно-активных веществ. С успехом можно использовать ванны, в которых процесс очистки проводится в поле ультразвука, что существенно увеличивает производительность и качество очистки поверхности.
Ванны для электрополировки
Для электрохимического полирования принято изготавливать специальные ванны. Помните, что они являются очень опасными для здоровья, особенно при высокой температуре. Для полировки изделий из цветных и черных металлов, в частности из углеродистой стали, самым популярным остается универсальный электролит.
Его состав такой: ортофосфорная кислота (65%), серная кислота (15%), хромовый ангидрид (6%), вода (14%). Режим работы: температура около 70-90 градусов по Цельсию, напряжение на уровне 6-8 В, анодная плотность тока примерно 40-80 а/дм2, выдержка 5-10 минут.
Электрополировку нержавеющей стали - хромоникелевой и хромоникельмолибденовой принято проводить в следующем растворе: ортофосфорная кислота (65%), серная кислота (15%), хромовый ангидрид (6%), глицерин (12%), вода (13%).
Режим работы данного раствора: температура порядка 45-70 градусов по Цельсию, анодная плотность тока близко 6-7 а/дм2, уровень напряжения 4,5-6 В. Выдерживают деталь в такой ванне 4- 30 минут: для штампованных изделий достаточно 4-6 минут, для деталей после термической обработки или сварки 10-12 минут, для литых отпескоструенных изделий из стали - полчаса.
Для полирования изделий из алюминия или его сплава применяют хорошо зарекомендовавший себя электролит такого состава: ортофосфорная кислота (65-70%), хромовый ангидрид (8-10%), вода (20-27%). Режим работы: температура на уровне 70-80 градусов, в свежеприготовленном растворе плотность тока должна достигать 10-30 а/дм2, в насыщенном солями растворе - 10-20 а/дм2. Выдерживают деталь 5 минут и больше.
Для электрополировки деталей из дюралюминия необходим такой состав раствора: серная кислота (40%), ортофосфорная кислота (45%), хромовый ангидрид (3%), вода (11%). Режим работы: температура в пределах 60-80 градусов Цельсия, анодная плотность тока на уровне 30-40 а/дм2, уровень напряжения 15-18 В, выдержка – пара минут.
Таким образом, при необходимости электрополировки деталей в домашних условиях вы можете пойти двумя путями – изготовить специальное оборудование с валом электромотора и полировально-шлифовальными кругами или оборудовать ванну полирования и приготовить нужный для данного случая электролит. Что ближе – выбирать вам!